Ultra fine cleaning with plasma cleaning
On almost all surfaces there are fine soiling invisible to the human eye, which severely impairs further treatment of surfaces such as gluing, printing, painting or coating. These fine impurities on metals, plastics or inorganic materials can be removed by plasma cleaning (ultrafinecleaning) without the use of additional chemicals. In contrast to plasma coating or plasma etching, the surface of the workpiece is not removed or additionally coated, but merely modified.
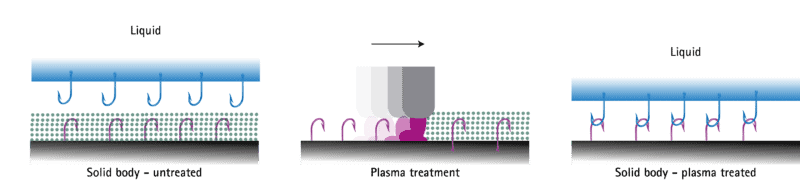
Ultrafine cleaning of surfaces with cold atmospheric pressure plasmas is a process of removing organic, inorganic and microbial surface contaminants, as well as strongly adhering dust particles. It is highly efficient and at the same time very gentle to the treated surface. At higher strength, it can remove weak surface boundary layers, cross-link surface molecules and even reduce hard metal oxides. Plasma cleaning promotes wettability and adhesion enabling a wide spectrum of industrial processes preparing surfaces for bonding, gluing, coating and painting. While being performed using air or typical industrial gases including hydrogen, nitrogen and oxygen, it avoids wet chemistry and expensive vacuum equipment, which positively affects its costs, safety and environmental impact. Fast processing speeds further facilitate numerous industrial applications.
Typical surface contaminants
Multiple layers of contaminants usually cover surfaces, even if the latter visually appears to be clean. Contaminants form naturally due to exposure to air. They include layers of oxides, water, various organic substances and dust. Furthermore, technological processes leave surfaces covered with oils, release agents, compounding ingredients, monomers and exuded low molecular weight species. Contaminants can drastically reduce the quality of the adhesive bonding by introducing a weak intermediate layer. Moreover, their typically low wettability results in incomplete surface covering by the adhesive, further reducing the bonding strength.
Advantages of plasma cleaning
As the plasma processes, initiated on the treated surface, break contaminants turning them into vapor, no residues are left on the surface, leaving the latter in the ultra-fine clean state. Most importantly, the plasma cleaning process works at atmospheric pressure. Its advantages comparing to standard chemical and vacuum plasma cleaning processes include:
- Ultra-fine cleaning, no residues
- Gentle surface treatment
- No wet chemistry
- Air or cheap non-toxic working gases
- Environmental friendliness
- No expensive vacuum equipment
- Fast processing speeds
- Easy integration into existing production lines
- Promotion of wetting and adhesion
Application exampes
Plasmacleaning – Article magazin “JOT”
Paint stripping and cleaning with plasma is possible with the high performance system plasmabrush® PB3 of relyon plasma.
Dr. Stefan Nettesheim from relyon plasma will give a presentation about cold plasma in disinfection technology at VDI.TECHNIK.TALK.ONLINE.
Application report: SITA Messtechnik GmbH
In the user report SITA Messtechnik has investigated the efficiency and effect of plasma cleaning of stainless steel by means of fluorescence measurement.
Customer reference: Dieter Braun GmbH
Dieter Braun GmbH reports about their expierience with plasma treatment of cables and wires before moulding and encapsulation.
Cleaning industrial parts with plasma
Industrial parts cleaning with plasma is an environmentally friendly and inline-capable cleaning technology that ensures high quality in downstream processes.