Pretreatment with plasma in rocket development
Space Team Aachen uses the piezobrush® PZ3 for pretreatment with plasma in rocket development. In an application report, the student association provides insight into the work with the handheld device and the results achieved.
Motivation for the use of plasma
In the STAHR (Space Team Aachen Hybrid Rocket) project of Space Team Aachen e.V., a student experimental rocket with a self-developed hybrid engine is being constructed. The project is supervised by DLR (German Aerospace Center) within the framework of the STERN program. DLR’s STERN program (Student Experimental Rockets) offers aerospace engineering students at German universities the opportunity to plan and build their own rocket projects and launch them from the Esrange Space Center in northern Sweden. The rocket will launch in late 2024 and fly at speeds of up to Mach 1.4 to an altitude of at least 10 km. Almost all components will be developed in-house, from the flight computer to the engine and structural components.
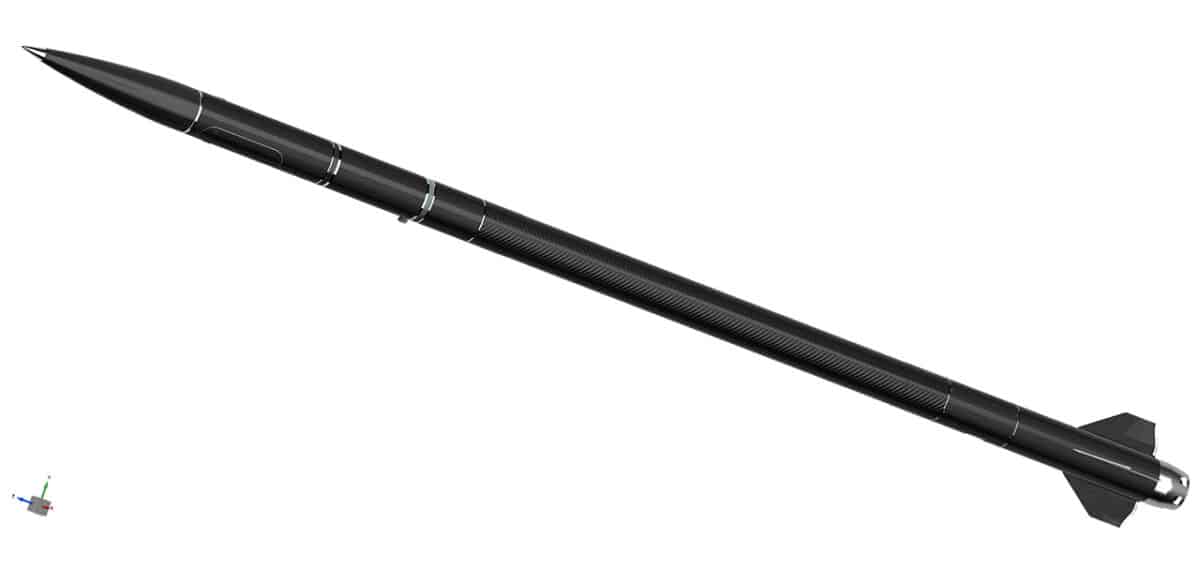
The main elements of the rocket structure are the so-called body tubes. These are tubes made of carbon and glass-fiber reinforced plastic. Each rocket section consists of one tube. The individual sections are connected by aluminum interfaces glued into the tubes. The glued connection from the tube to the interface is a critical connection in the rocket. If it fails, the flight is a failure.
To achieve the best possible joint strength, suitable surface pretreatment of the bonding surfaces is essential. As part of a series of tensile shear tests in accordance with DIN 1465 at the Institute of Welding and Joining Technology (ISF) in Aachen, we first tested various pretreatments. Sandblasting on the aluminum interface and pretreatment with plasma on the carbon fiber-reinforced plastic (CFRP) proved to be the most suitable. For the plasma treatment, we used the piezobrush® PZ3 handheld plasma device at the institute. Its small form factor makes the device perfect for use inside the rocket’s carbon fiber tubes. It can also be taken anywhere in its carrying case, which is important for us since we work at different institutes in Aachen and thus need to be mobile.
Production of a section prototype
In order to experimentally validate the structure of the rocket, we made a prototype rocket section. The prototype consists of a carbon fiber reinforced tube bonded to two aluminum interfaces. This was the first time we used the piezobrush® PZ3 plasma handheld device on a real rocket component. Before surface treatment, we thoroughly cleaned all bonding surfaces with isopropanol. The pretreatment of the inside of the carbon fiber reinforced tube worked very well. The compact size of the unit made surface activation inside the tube possible in the first place.
Alternative pretreatment methods such as lasering would be difficult to implement due to the limited space. On the recommendation of Relyon Plasma, we used the device not only for surface activation of the carbon fiber-reinforced tube, but also for additional cleaning of the sandblasted surface of the aluminum interface. Here we initially had the problem that the device switched off the plasma after a few seconds. However, a quick look at the manual quickly remedied the situation: The shutdown is a protective function, which is activated if the device does not make contact with the component within five seconds. With this function in mind, further handling of the interface worked without a hitch. Results of the test series, for which we produced the prototype, are not yet available. These will be carried out at the end of August.
Due to the practical handling and the compact form factor, which is important for our application, we have firmly integrated the use of the piezobrush® PZ3 plasma handset into our production process.
About Space Team Aachen
Space Team Aachen is an association that offers interested students of RWTH and FH Aachen the opportunity to participate in pioneering space research. The growing team currently consists of more than 140 members. They are developing their own hybrid and liquid rocket engines. In addition, the highly motivated researchers also participate in international rocket competitions with their innovative developments. The team works closely with numerous renowned partners from science and industry.