Plasma treatment of polymer base plates for 3D printing
Students at the Technical University of Lübeck work at the Laboratory for Surface Technology with the plasma handheld device PiezoBrush PZ3. Here, the students investigate the effects of plasma treatment on the adhesive strength of 3D printing on polymer base plates. These serve as carrier plates for 3D printing of polymer components. Good adhesion is necessary to prevent the “wrap effect” – the partial or complete detachment of the print object from the printing plate during the printing process. This detachment causes the objects to move when passing over the extruder, resulting in the failure of the print. After completion, however, the printed object must still be easy to detach so that no damage occurs to the finished object.
Currently, the base plates are sprayed with adhesive spray to achieve this result. In addition, there are special base/support plates with very good adhesive strength, which are, however, relatively expensive. In the experiment, inexpensive and easily available polyethylene plates (PE) are treated with atmospheric pressure plasma from the PiezoBrush PZ3, which do not provide sufficient adhesive strength without plasma treatment.
Experimental setup
The figure shows three printed components (green) made of polylactide (PLA) on polyethylene plates (PE), showing excellent print quality. In the top left field, the carrier plate was cleaned with isopropanol only. Printing was impossible here.
The polyethylene plates on the top right were treated with atmospheric pressure plasma from the PiezoBrush PZ3 and show very good adhesion.
The base plate at the bottom left was cleaned with isopropanol and then treated with the dimafix adhesive spray. The 3D print adheres very well here as well.
The combination of cleaning, adhesive spray and additional atmospheric pressure plasma at the bottom right also achieves a very good result, but no greater adhesive strength than with plasma or adhesive spray alone.
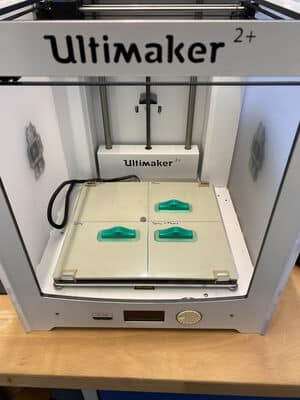
The experiment shows: a single treatment with atmospheric pressure plasma at low power is sufficient to make the non-polar polyethylene surface polar by incorporating oxygen into the surface, for example, and to print with the polar polylactic acid (PLA). The adhesive strength is sufficient but not too high, so that a non-destructive removal of the component is possible. This eliminates the need to purchase adhesive spray and very expensive carrier plates, especially if the PiezoBrush PZ3 is already in use. In 3D printing, the plasma handheld device is used primarily for bonding 3D-printed individual parts into larger components or for surface activation and plasma cleaning of substrates prior to 3D printing.
Further applications in 3D printing
Plasma treatment of polymer base plates
At the TH Lübeck, a plasma treatment of polymer base plates is carried out before 3D printing in order to achieve good adhesion.
Case Study: University of West Bohemia
University of West Bohemian reports about the plasma treatment of gold and copper electrodes for environmental and biomedical applications.
Reference: University of Stuttgart
At the University of Stuttgart the plasma handheld device piezobrush® PZ3 is used for plasma activation in 3D printing for microoptics.
Plasma in additive manufacturing
From 19 – 22 November 2019, formnext, the world’s leading trade fair for additive manufacturing will take place in Frankfurt am Main. Relyon plasma will present in hall 11 on booth A76 which adhesion improvements are achieved by plasma in additive manufacturing.
Reference University of West Bohemia
The University of West Bohemia reports on the integration of the high performance plasma system plasmabrush PB3 into an aerosol jet system for 3D printing.