PlasmaBrush PB3
High-performance atmospheric plasma system
The PlasmaBrush PB3 is our high-performance plasma system for all inline processes in industrial and high-speed applications. The PlasmaBrush PB3 is widely used in the automotive, packaging and printing sectors. The focus here is primarily on plasma cleaning and surface activation. This is primarily used to prepare the products for further downstream processes such as bonding, painting or printing.
The PlasmaBrush PB3 is a combination of a particularly compact and long-term stable plasma generator in nozzle form, a unipolar pulsed high-voltage source and a vortex flow in the nozzle. The perfectly matched components in a robust industrial design are perfect for easy integration into any system.
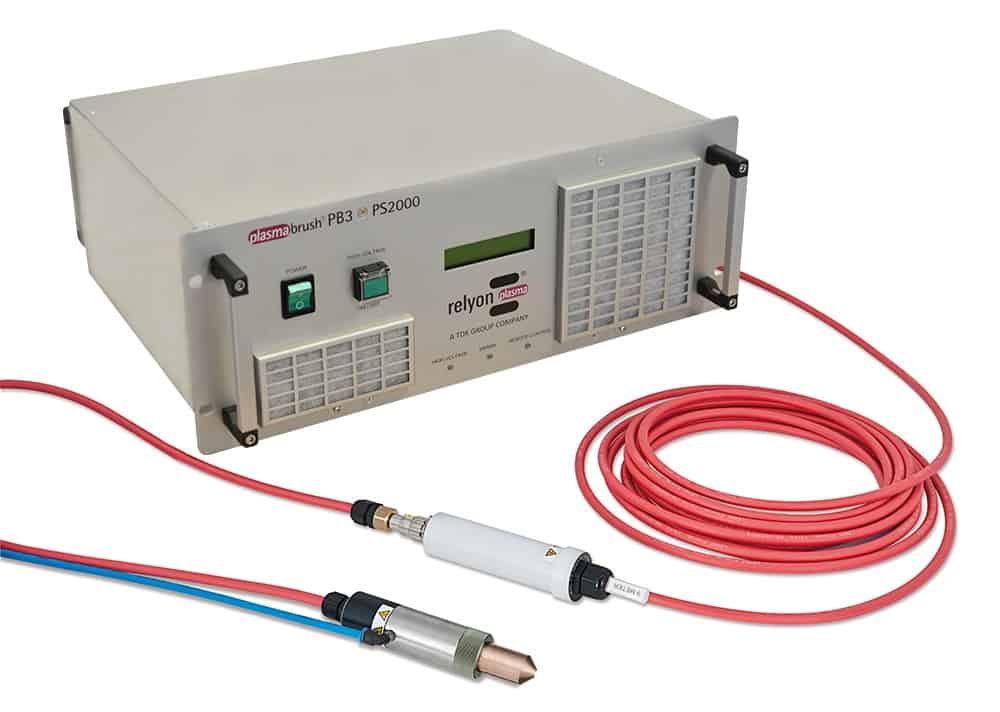
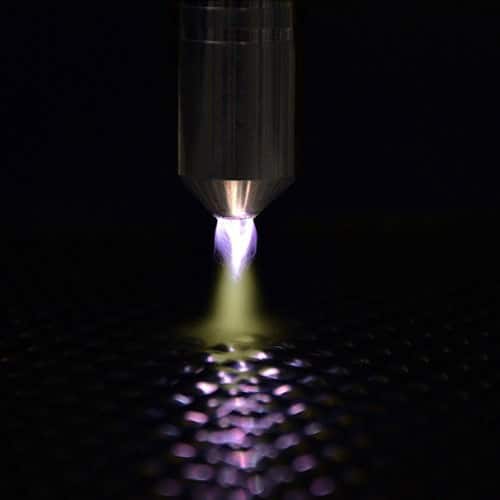
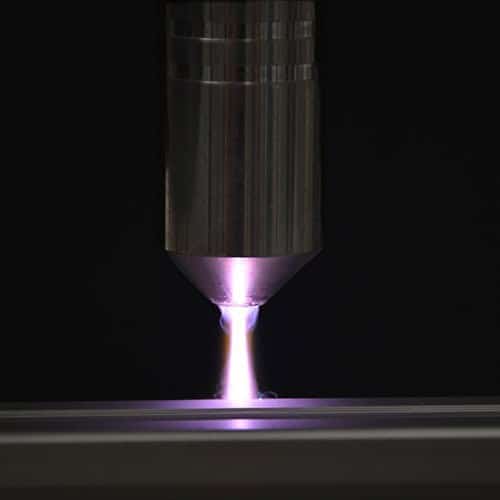
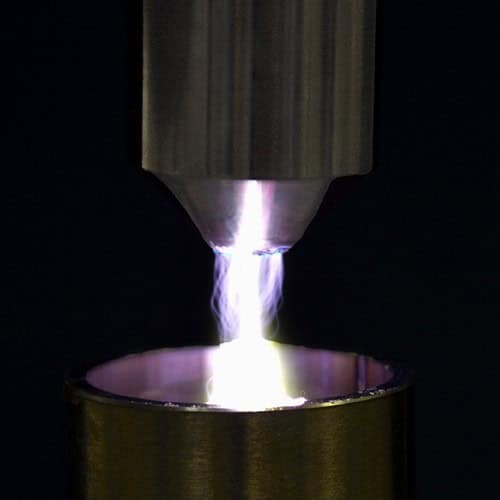
Application technology
Field of application
- Automotive sector
- Printers and printing industry
- Packaging industry
Applications
- Ultrafine cleaning
- Reduction of oxide layers
- Surface functionalization
- Pre-activation for bonding, sealing, casting or printing
- Coating, laminating and sealing
- Germ reduction and sterilization
- Print pre-treatment
The table below shows the surface energy of different plastics. In each case, the surface energy is shown after treatment with the PiezoBrush PZ3, the PlasmaBrush PB3 (plasma high-performance system) and without prior plasma treatment.
Advantages
- Very compact design, also suitable for narrow grooves and hard-to-reach areas
- Easy integration even in small robots (
- Suitable for compressed air, nitrogen and other gases
- Variable Power
- High start-stop dynamics
- Maximum operating reliability
Customer references
Grounding of conductive substrates
When using PAA® technology, the ignited plasma bridge can be used for electrical grounding of conductive substrates.
Product change for nozzle improvement
The A250, A350 and A450 nozzles used in conjunction with the plasmabrush® PB3 have undergone a material change. As a minor product change for nozzle improvement, the copper nozzles will be nickel-plated from February 2022.
Visualization of Activated Area on Polymers
A visualization of activated area on polymers is done with test ink to evaluate atmospheric pressure plasma jets (APPJ). The shrinkage characteristics of the test ink are collected using activation image recording (AIR).
Customer reference: Solar thermal energy
GREENoneTEC uses atmospheric pressure plasma in solar thermal technology to increase surface tension and process-safe bonding.
PlasmaBrush PB3 in our Online Shop
-
Rental unit PlasmaBrush PB31.000,00 € / 29 days
zzgl. Versandkosten
-
PlasmaBrush PB3
Technical Data
- Flow range: 35 to 60 l/min
- Weight plasma generator: 680 g
- Gas connector: 6 mm
- Treatment speed: 0,1 – 2 m/s
- Typical treatment distance *: 10 – 25 mm
- Typical treatment width *: 15 – 25 mm
- Power consumption power source PS2000: ~ 1000W
*Typical treatment parameters depend strongly on the application, utilised nozzle and process gas.
Nozzles PlasmaBrush PB3
There are three different nozzles for the PlasmaBrush PB3 atmospheric pressure plasma generator. All nozzles are high performance nozzles which are operated with a Pulsed Atmospheric Arc (PAA®) Plasma Generator (PG31) and pulsed high voltage power supply (PS2000).
The nozzle achieves the following functions:
- focussing of the plasma flame
- acting as a grounded cathode to confine the highpower electric arc
- forming of the cavity to excite the process gas
Nickel-plated nozzles
Nozzle A 250
Field of application:
- Surface cleaning
- Surface activation
- Optimized for electric potential-free processes
Although the copper nozzles originally used have very good properties in terms of burning behavior, there were customer requests to improve the oxidation resistance on the outside. This is essentially only an optical effect without any influence on the burning behavior, but it was nevertheless not possible to ensure that no oxide particles would detach from the nozzle and thus contaminate the workpiece. As a result, relyon plasma tested the copper nozzles again in a large-scale series of tests in order, among other things, to prevent the copper oxide from forming on the surface. For this purpose, very good results were achieved by nickel-plating the nozzles, which also prevents the formation of the surface oxides and the associated problems in the long term. In the tests it was shown that the coating does not lead to any impairment of the burning properties and the operating parameters. In the future, relyon plasma will therefore offer nickel-plated copper nozzles as a fully-fledged replacement for the copper nozzles offered to date.
Nozzles in our Online Shop
-
Nozzle A250325,00 €
-
Nozzle A350325,00 €
-
Nozzle A450325,00 €
Carbide nozzles
The most commonly used nozzles in the PlasmaBrush PB3 so far are the copper nozzles. In processes where the arc is transferred to the substrates, e.g. when cleaning or reducing metal surfaces, the copper nozzles have a very long lifetime*. When polymers are surface activated, however, the arcs dock to the lip of the nozzle, resulting in a shortened service life due to erosion.
In order to extend the lifetime of the nozzles in this popular operating mode, relyon plasma has now developed the special nozzles with a carbide core.
Due to the material properties of carbide, the carbide nozzles are much more resistant to oxidation and erosion than the standard copper nozzles. Thus, even in the treatment of polymers, a 4-fold higher nozzle lifetime could be achieved than with the copper nozzles. Due to the significantly longer service life of the nozzles, the process now requires less maintenance, is more sustainable and more stable.
Another field of application for carbide nozzles is in the semiconductor industry, where the copper abrasion of standard nozzles is often problematic. This can also be prevented by using carbide nozzles.
*At this point we expressly refrain from publishing diagrams or tables of the life expectancy of nozzles determined under laboratory conditions. These data were misleading for the consumer, because different process influences as not calculable factors strongly impair the life span.
Nozzle A 351
Field of application:
- Surface cleaning
- Surface activation
- Thermal treatment and reactive coating
- Optimized for sensitive materials
Nozzle A 451
Field of application:
- Surface cleaning
- Surface activation
- Thermal treatment and reactive coating
- Optimized for high process speeds
Technology
Our PlasmaBrush can be adapted to fit process requirements spot-on through a wide variety of accessories. Thus, the quality of your processes and products can be optimized at minimal cost. You only use the components you really need. All components are coordinated perfectly and have been through extensive stress tests. This simplifies maintenance and servicing, and availability is ensured on the shortest possible time scale.
We have consciously adapted our high voltage power supply PS2000 to the independent industrial standard of CanOpen, which makes exceedingly reliable communication possible even under the more severe circumstances an industrial environment can bring about.
A great number of sensors or mass flow controllers operate using the same standard. Every prevalent industrial control worldwide provides a suitable interface. Up to 127 devices can be addressed via CAN node. Every PS2000 high power source can be controlled with a simple DIP switch in the address space of 0 to 99.
PS2000 High voltage source
The PS2000 High voltage source optimised for Pulsed Atmospheric Arc Technology (PAA Technology®). Due to the use of a unipolar pulsed high voltage, the arc is prevented from stabilising at “hot spots” in the nozzle. The latest IGBT switching technology and the use of high quality high voltage components ensure that the source is extremely reliable and efficient. Overloading is also not possible in continuous 24/7 operation. In the event of cable damage or short circuiting during critical operations the control unit intercepts all power fluctuations safely.
The capability of the PS2000 is particularly reflected in the fact that it can operate with variable loads and can effectively pump loads within a large potential range of up to > 12 kV. This special feature ensures continuous ignition performance across a wide power range and for different process gases. The high voltage source is switchable in a range of milliseconds at full load and therefore optimised for timed processes where highly precise timing is beneficial.
All communication is based on the reliable and fast CAN bus. Even in the event of a fault, the communication remains active. Integration into each automated production plant is simple and standardised, even in the case of several high voltage sources.
Performance features:
- Input voltage: 220 – 240 V AC, 50-60 Hz
- Max. input current: 6A
- Weight: 18 kg
- Power: 1,000 Watt
- Open circuit voltage: up to 20 kV
Integration packages PlasmaBrush PB3
In principle, you need a power supply, compressed air supply (alternatively, nitrogen or forming gas can also be used) and an extraction system for safe operation to commission the PlasmaBrush PB3 system. All other components you need for commissioning are available from us directly from a single source.
Emergency stop switch
An emergency stop switch is mandatory for the use of the PlasmaBrush PB3 system in order to ensure work safety. The emergency stop switch of the pre-existing system can be used here. Alternatively, the emergency stop switch can be purchased from relyon plasma and installed directly on the power source PS2000.
Gas supply package
The gas supply package includes a moisture filter, oil filter and a particle filter as well as a pre-adjusted throttle. This is the minimum requirement for regulating the gas flow. Please note that the gas supply package is not a flow regulator and therefore does not provide any process control.
Communication Package
The PlasmaBrush PB3 system can be operated as a basic system with one plasma generator PG-31 and one power source PS 2000 or as a multiple system with several plasma and power sources – depending on your individual requirements. In principle, the plasma can also be activated manually via the integrated toggle switch or controlled using a communication package. Various packages are available here.
Communication Package Digital I/O
Communication Package USB
Communication Package CAN
Communication Package ProfiNet
FAQ
Downloads
Plasma generator PG31
Description | Language | Download |
---|---|---|
PlasmaBrush PB3 Flyer | EN | Flyer |
Plasma Generator PG31 Manual | EN | Manual |
Plasma Generator PG31 Manual | ES | Manual |
Plasma Generator PG31 Manual | FR | Manual |
Plasma Generator Nozzle Change | EN | Nozzle Change |
PlasmaBrush PB3 Paper | EN | Paper |
Plasma source PS2000
Description | Language | Download |
---|---|---|
PS2000 Manual | EN | Manual |
PS2000 Manual | DE | Manual |
PS2000 Manual | ES | Manual |
PS2000 Manuel | FR | Manuel |
PS2000 Quick Start Guide | EN | Quick Start Guide |
PS2000 Quick Start Guide | DE | Quick Start Guide |
PS2000 Software (eds) | EN | PS2000 Software (eds) |
Communication packages
Description | Language | Download |
---|---|---|
Manual Communication Package CAN | EN | Manual Communication Package CAN |
Manual Communication Package CAN | ES | Manual Communication Package CAN |
Manual Communication Package CAN | FR | Manual Communication Package CAN |
Manual Communication Package USB | EN | Manual Communication Package USB |
Manual Communication Package USB | ES | Manual Communication Package USB |
Manual Communication Package USB | FR | Manual Communication Package USB |
Software Communication Package USB | EN | Plasma control V2.6 |
Manual Communication Package ProfiNet | EN | Manual Communication Package ProfiNet |
Software Communication Package ProfiNet | EN | Software Communication Package ProfiNet |
Manual Communication Package Digital I/O | EN | Manual Communication Package Digital I/O |
Manual Communication Package Digital I/O | ES | Manual Communication Package Digital I/O |
Manual Communication Package Digital I/O | FR | Manual Communication Package Digital I/O |
Nozzles
Description | Language | Download |
---|---|---|
Data Sheet Nozzles | EN | Data Sheet Nozzles |
HVC Cable Extension
Description | Language | Download |
---|---|---|
Cable Extension Manual | DE | Cable Extension Manual |
Cable Extension Manual | EN | Cable Extension Manual |
Cable Extension Manual | ES | Cable Extension Manual |
Cable Extension Manual | FR | Cable Extension Manual |
Cable Extension Manual | JP | Cable Extension Manual |
Cable Extension Manual | IT | Cable Extension Manual |
Cable Extension Manual | PT | Cable Extension Manual |